Before their deep energy retrofit, David and Krista Claus and their three teens lived in a fair bit of discomfort in their house in Prince George, B.C. Cold winters caused condensation to freeze beloved stuffed animals to walls, and the family’s cherished tropical fish went belly-up during a heat dome.
Before building the addition or upgrading the mechanicals and the existing envelope, the Claus house used 127 GJ a year—36 GJ more energy than the average for a new size-comparable house at 91 GJ a year. After the deep retrofit and expansion their house was comparable in size with new houses that would typically use about 125 GJ a year. — But the Claus house now uses less than half of that at just 58 GJ a year. Their deep energy retrofit achieved 54% in energy savings despite almost doubling the livable indoor space!
Retrofit at a Glance | |
Starting Point | Retrofit Results |
127 GJ EnerGuide Rating | 58 GJ EnerGuide Rating (54% energy savings) |
Air-leakage rate of 6.2 ACH50 | Air-leakage rate reduced 84% to 0.6 ACH50 |
Attic insulation R19/28 | 88% of attic now >R80 |
Wall insulation mostly R12 | Wall insulation to R48 (cellulose & mineral wool) |
Basement insulation R8 | Basement walls now R39; basement floor R32 |
/ | High-performance fibreglass doors |
/ | Heat loss reduced by 61% |
95% efficient condensing gas furnace | Added an air-source heat pump for heating and cooling |
/ | Added an ERV |
Built 1924 | Retrofit 2023-2024 |
/ |
GHGs down 93% |
The Home Retrofit Journey
The Claus household’s retrofit journey all started when they were house hunting and realized that they just loved the location where they already were. Originally, Krista was not interested in the hassle and disruptions that come with a typical home renovation and just wanted to go on vacation. However, the rattling windows, drafty rooms, and general indoor discomfort finally led Krista to ask David why they hadn’t started on an energy retrofit of their home yet.
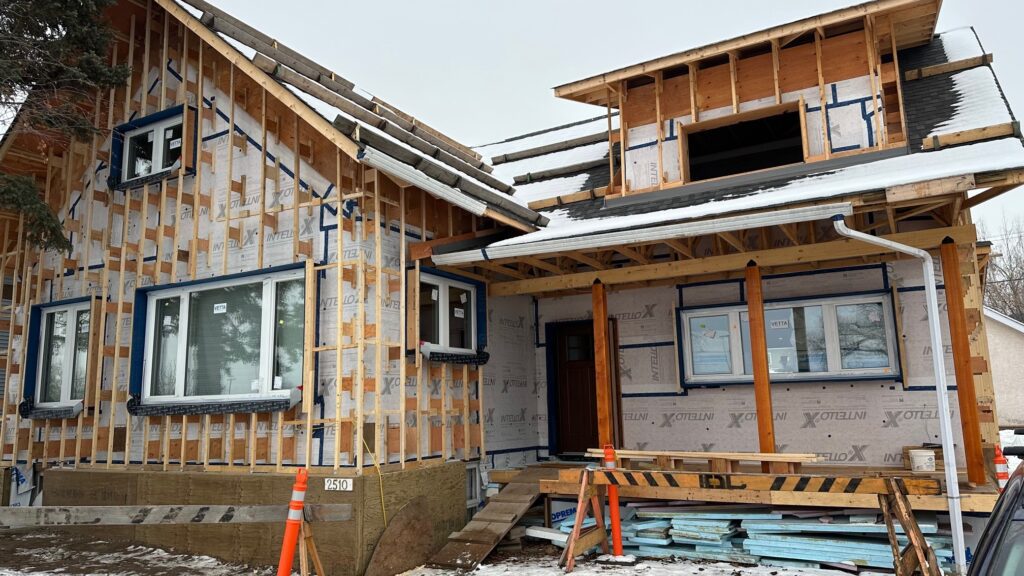
Larsen trusses to support external application of additional insulation to the exterior walls.
David is a building science professional, so he took it upon himself to plan and redesign their family’s dream home. For those who want what the Claus family achieved for their own house, it is important to get the right expertise to help you with your retrofit project—whether that be from a green architect, energy advisor, or another comparable building science professional. Green builders were invaluable for David’s home retrofit project but not essential—he was available to stand in to supervise contractors who were less familiar with certain green building products, techniques, or standards.
The work on the Claus house started in May of 2023, with an intentional focus on waste reduction through re-use and recycling of materials. David’s plan was to keep as much of the existing structure as possible—especially the concrete foundation—as they renovated, retrofitted, and expanded the footprint. David was able to salvage and reuse most of the wood, and whatever wasn’t reused was carted off to be recycled.
When replacing the roof, the hundred-year-old rafters were made of exceptionally good-quality 20-feet two-by-four planks of old-growth Douglas fir, which were reclaimed and reused. These decisions not only helped save on costs of buying new materials, but also on the embodied material carbon from production and transport of new materials. David had initially planned to use only blown cellulose insulation not only to avoid manufacturing emissions but also to sequester carbon by locking it away in the envelope of the building. Leftover loose-fill mineral fibre insulation from a university lab construction was also integrated into their renovation. This saved on some cost and diverted would-be construction waste from going to the local landfill.
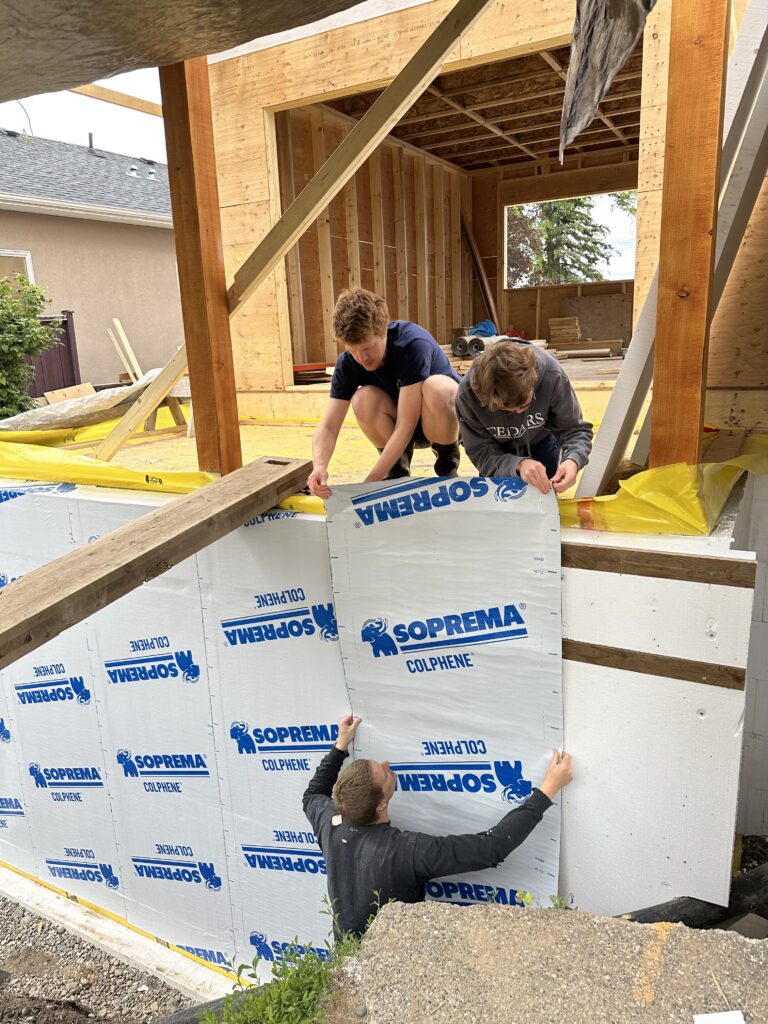
Contractors insulating the extended foundation of the house.
After the new windows and doors were put in place, draft-proofing and insulation followed in the autumn of 2023. All of the insulation and draft-proofing work was done from the exterior while the family was still living inside their home. The times when construction came into the home were when electrical needed moving and when new openings and supports for windows were being made.
The basement and foundation walls were accessed by excavating around the exterior and insulated with expanded polystyrene (EPS) boards at 80% coverage. The main-floor walls were insulated from the exterior with 10 inches of mineral wool at 84% wall coverage within Larsen Truss framing, while the attic was insulated with blown cellulose.
When opening the walls to add structural elements, David was pleasantly surprised to not find mould in the walls that had experienced condensation issues. The same could not be said for the house’s old cathedral ceiling, which was unvented, and some of the rafters had become covered with mould. David decided to have the entire roof replaced, raising it to get a proper air barrier under it and adding more headroom for the top floor.
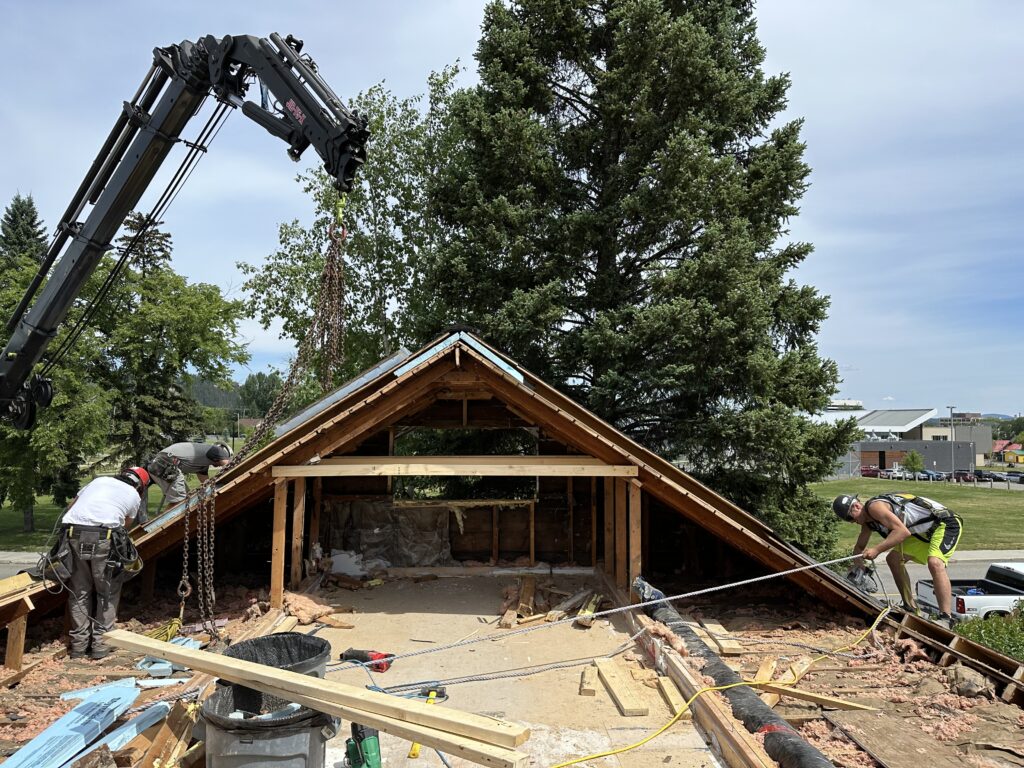
Replacing the old roof of the Claus house
The Claus house’s furnace worked hard to heat their home in past winters because the envelope leaked like a sieve and, as a result, the indoor air became very dry. The air-source heat pump and an energy recovery ventilator (ERV) were installed in the spring of 2024. The Claus family also uses an on-demand tankless gas boiler as an auxiliary heating system in the unlikely case that their heat pump is unable to heat the house.
“I just put that gas boiler in three or four years ago,” explains David.. “I run, what I like to call, ‘the world’s smallest district energy system.’ The gas boiler allows me to also heat my garage and a greenhouse—which are separate buildings.”
The Retrofit’s Benefits
Summers get toasty up in Prince George, and wildfires are now more common. The Claus family got a heat pump to cool and an ERV to mechanically ventilate the house. Normally, the Claus family would open windows to create a cross-breeze. Windows, however, aren’t able to filter harmful pollution and ash as a properly maintained ventilation system would. With a much tighter building envelope, the house became stuffy during the depths of winter, and the family would open windows to find relief. After installation of the ERV, fresh air was brought in without needing to open the windows. The ERV filters and pre-heats the fresh air by transferring heat from the exhausted stale air. Cleaner air coming in through the ERV rather than through scattered cracks and gaps, resulting in a build-up of soot and dust behind baseboards and floorboards, provides significantly healthier indoor air quality and superior comfort.
In winter, pipes in the bathrooms no longer freeze, moisture no longer condenses on the walls of the washrooms and the stairwell, and ice no longer forms on windows. The constant flow of fresh air provided by the ERV helps prevent condensation and balance humidity levels. After insulating the foundation, the basement is warm and dry and the damp and musty smell is gone. The Clause house had a problem with ladybugs overwintering in their home, but since leak-sealing their envelope, they have not had a repeat infestation. On top of that, Grandma can now braise beets from Grandpa’s farm for Christmas without beet juice condensing and running down cold walls! Stuffed animals and pets alike are now safe. This once a leaky house has become an energy-efficient home.
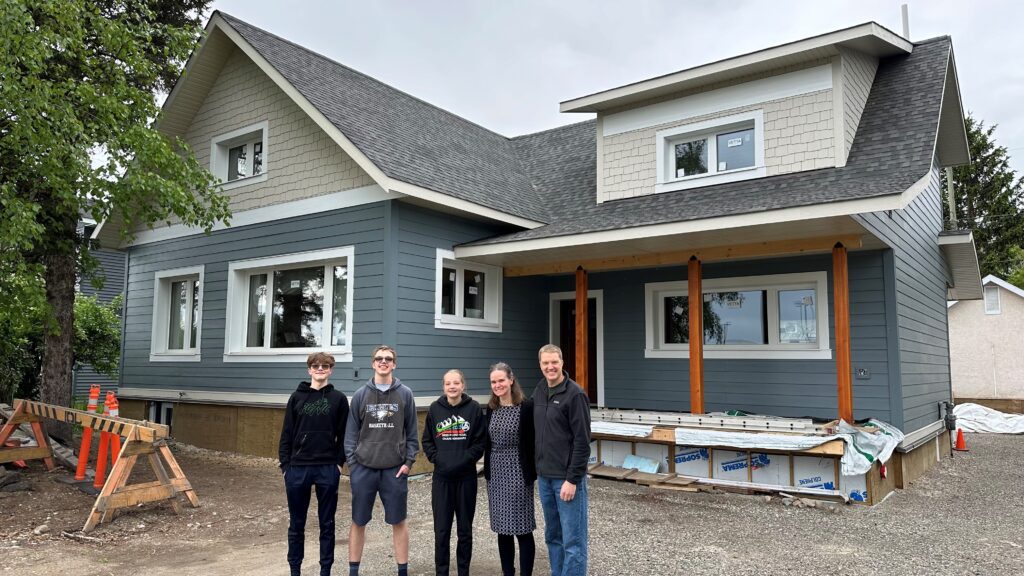
The Claus family amid the finishing touches of their retrofit and expansion.
Financial and Climate Goals
When the Claus family set out to fix their century-old house, David was set on reaching Passive House’s EnerPHit retrofit certification and has nearly achieved it, only now needing to insulate the basement floor slab. In that future home renovation project, David would also like to update the plumbing and add another washroom.
“We wanted to reuse as much material as we could,” explains David, “We wanted to bring down the energy intensity and the carbon footprint of the house. We also looked at the toxicity level of the materials that we put in, to some degree.”
To David and his family, health, comfort, and ecological impact were the driving forces of why they embarked on a deep energy retrofit journey to update their home.
When asked about what would have helped make his deep energy retrofit journey smoother, David relayed that streamlining rebate programs, growing the green design community, and increasing the availability of green builders in the trades and construction market would have saved him a lot of time and hassle.
Recent Comments